350.000 Datensätze weltweit aktuell verfügbar
Im Rahmen des RiPrio-Projekts führt Rittal derzeit eine durchgängige Konfigurationslösung auf Basis des EPLAN Engineering Centers (EEC) seines Schwesterunternehmens EPLAN ein.
In der AprilAusgabe berichtete der CADCAM REPORT über das Projekt RiPrio, mit dem Rittal eine durchgängige Konfigurationslösung für seine Schaltschränke, Stromverteilungen sowie ITInfrastrukturProdukte aufbaut. Die dort beschriebene Konfiguration mit dem EPLAN Engineering Center bedarf einer einheitlichen CAD und vor allem PDMUmgebung, damit sich alle im Rahmen eines Auftrags anfallenden Dokumente für vorgedachte Varianten vollautomatisch erstellen lassen. Der hier folgende zweite Teil des Beitrags zum RiPrioProjekt beschreibt die Konsolidierung der CAD und PDMUmgebung mit Unterstützung des Schwesterunternehmens EPLAN. Keine einfache Aufgabe, denn über 350.000 technische Datensätze sind einzupflegen, um diese weltweit in der jeweils aktuellsten Fassung abrufbar zu machen. Im Rahmen des RiPrio-Projekts führt Rittal derzeit eine durchgängige Konfigurationslösung auf Basis des EPLAN Engineering Centers (EEC) seines Schwesterunternehmens EPLAN ein (siehe CAD-CAM REPORT 4/2012, S. 28). Während das Produktregelwissen für das gesamte Produktportfolio des Herborner Unternehmens sukzessive im EEC abgebildet wird, wird das Produktionsregelwissen weiter in der SAP-Konfigurations-Lösung verwaltet. Um die für die Produktbeschreibung als auch für die Produktion erforderlichen technischen Daten zur Verfügung zu stellen, installiert Rittal unternehmensweit Autodesks PDM-Lösung Vault Professional für rund 500 User weltweit. Produktionsstandorte wie Italien oder die USA sind in den nach Einschätzung von EPLAN größten Vault-Rollout Europas integriert. „Wir sprechen hier von über 350.000 technischen Datensätzen – vor allem 3D-Modellen, 2D-Zeichnungen und Stücklisten – die wir steuern müssen“, erläutert Bernd Lehnert, Abteilungsleiter FuE bei Rittal in Herborn und zuständig für Technologie & Support. „Voraussetzung dafür ist eine PDM-Lösung als einheitliche Informations- und Managementbasis für alle technischen Produktdaten.“ Ist zukünftig das Produkt-Know-how im EEC hinterlegt, kann Rittal seine Produkte effizient konfigurieren und Aufträge weitestgehend automatisiert abwickeln. „Unser Ziel ist es, sämtliche technischen Auftragsdaten automatisch zu erzeugen“, so Lehnert weiter. „Das läuft zunächst über das EEC – hier steckt die Konfigurationslogik –, aber das PDM-System muss natürlich die Basisdaten liefern.“ Dazu gehörten neben Stücklisten und Arbeitsplänen auch die CAD- sowie die NC-Daten für die Fertigung. Analog gilt das auch für die optional angebotene Montage von Zubehör, das mehr als 5000 Artikel umfasst – gerade in diesem Bereich will man den Kunden zukünftig die Wahl der jeweils passenden Ausstattung so leicht wie möglich machen. „Der manuelle Aufwand in der Auftragsabwicklung soll aber über den zugelassenen Variantenraum hinweg weitestgehend reduziert werden.“ Was das konkret bedeutet, lässt sich gut am Beispiel der Kompakt-Schaltschränke des Typs AE erkennen, deren Logik bereits in das EEC eingepflegt ist. Die Schaltschränke – als Serienprodukt – lassen sich nicht nur hinsichtlich der Ausrüstung konfigurieren, auf Wunsch inklusive der Montage des Zubehörs, sondern auch bezüglich der Rohbearbeitung und kundenspezifischen Lackierung. Möchte ein Kunde Ausbrüche – etwa für Lüfter oder Taster – nicht selbst realisieren, kann Rittal dies für ihn individuell übernehmen. Denn das lässt sich nicht nur im Rohteil leichter fertigen, sondern bietet auch Vorteile bezüglich des Korrosionsschutzes, da die Lackierung erst danach erfolgt. „Entscheidend aber ist wiederum, dass wir in diesem Ablauf manuelle Tätigkeiten vermeiden wollen“, betont der FuE-Abteilungsleiter. „CAD-Modell, Zeichnungen, Stückliste, Arbeitsplan, Kalkulation und NC-Daten werden automatisch erzeugt – das führt zu deutlich effizienteren Abläufen.“ Auch lassen sich künftig vollautomatisch Zeichnungen für die Fertigung und Qualitätssicherung generieren, in denen die wichtigen Maße enthalten sind. Das zu montierende Zubehör kann in der Folge eindeutig den relevanten Ausbrüchen zugeordnet werden. ITIntegration als Herausforderung
Bei der Umsetzung der Strategie des RiPrio-Projekts ist vor allem die Integration der EDV-Systeme gefragt. „EEC, CAD, PDM und ERP müssen miteinander vernetzt werden, gerade auch, weil wir ja CAD-Zeichnungen automatisch erstellen wollen – wir müssen also sicherstellen, dass CAD-seitig die technische Datenbasis verfügbar ist“, fährt Bernd Lehnert fort. „Dieses Zusammenspiel zu ermöglichen, ist eine echte Herausforderung, denn schon die Definition des Lastenheftes war entsprechend komplex.“ Hintergrund ist, dass Rittal im Rahmen von RiPrio auch die gesamte Organisation optimiert, was voraussetzt, dass zuvor alle Arbeitsabläufe zu überprüfen und gegebenenfalls zu modifizieren waren – mit entsprechenden Auswirkungen auf die Struktur des Unternehmens bis hin zur Qualifizierung der Mitarbeiter. Auch rein CAD-seitig gab es einiges zu tun, denn bis Anfang 2000 gab es kein Standardsystem im Unternehmen. Zum Einsatz kam vorwiegend Autodesks AutoCAD, da die 2D-Bearbeitung für die vielen Blechteile meist ausreichend war. Ebenfalls genutzt wurden aber auch Autodesk Inventor sowie Catia und Pro/Engineer – insbesondere bei den komplexer werdenden Produkten wie IT-Racks mit Klimatisierung. „In der Summe ergab sich eine sehr heterogene Systemlandschaft bei uns“, erinnert sich Lehnert. „Wir entschlossen uns deshalb, standardmäßig die Autodesk-Produkte Inventor und AutoCAD einzusetzen.“ Sie bieten den Konstrukteuren von Rittal – bezogen auf das Produktspektrum – alle erforderlichen Funktionen, so dass sie unter anderem mit einem guten Preis/Leistungs-Verhältnis punkten können. Zur Zeit werden die Daten aller aktuellen Katalogprodukte im Inventor vereinheitlicht, andere Systeme werden nur noch für OEM-Kunden und Altdaten vorgehalten, falls daran Änderungen vorzunehmen sind. „An der Stelle müssen auch die CAD-Hersteller noch einiges tun, damit komplette 3D-Modelle mit der gesamten Hierarchie austauschbar werden – da sind die Systeme immer noch relativ geschlossene Welten“, sagt der FuE-Chef. Über Neutralformate wie STEP ließen sich zwar viele Daten austauschen, aber insbesondere bei komplexeren Modellen gingen auch Informationen verloren, gerade die Hierarchie betreffend. CAD und PDM sind eng gekoppelt
Mit der Wahl der Autodesk-Produkte war auch bereits eine Vorentscheidung bezüglich des PDM-Systems gefallen. „Dieses benötigt immer eine gute Schnittstelle zu den CAD-Lösungen im Unternehmen, damit es eine hohe Akzeptanz erfährt – und damit relevant wird“, so Bernd Lehnert. „Will heißen: Ohne eine vernünftige Schnittstelle und einen vernünftigen Ablauf in der Steuerung erreicht man keine Akzeptanz der Systeme.“ Das CAD-System müsse automatisch auf die Datenbank zugreifen und vor dem Herunterfahren die Daten auch wieder Einchecken – diese Integration sei wichtig. „Bei Lösungen von Drittanbietern ergibt sich hier häufig ein hoher Mehraufwand, um Schnittstellen anzupassen und eigene Anforderungen umzusetzen – insbesondere auch beim Update eines Teilsystems“, erläutert der IT-Profi. Vorteilhaft für Rittal war, dass mit dem Schwesterunternehmen EPLAN, das ja bereits über die Installation des EEC in RiPrio eingebunden war, Beratungs-Know-how und Dienstleistungen rund um Vault und Inventor zur Verfügung standen. „Gerade bei dem über viele Jahre gewachsenen Produktprogramm von Rittal findet man am Markt keine IT-Lösung, die hundertprozentig zu unseren Anforderungen passt – deswegen benötigen wir an dieser Stelle kundenspezifische Anpassungen“, betont Lehnert. Auf diese Weise ließen sich Erweiterungen der Funktionen ‚nachrüsten‘. So werden etwa auch die NC-Daten unter dem Produkt abgelegt, um eine effiziente Arbeit der NC-Programmierer zu erleichtern. „Das alles steigert die Benutzerfreundlichkeit und damit die Akzeptanz.“ EPLAN war auch bei der Altdatenübernahme involviert. Denn die rund 350.000 Datensätze wollte man ja möglichst automatisiert in die neue PDM-Lösung übernehmen. Vorab waren allerdings die Daten aus mehreren CAD-Lösungen – und zudem verschiedenen Versionen eines Systems – zu vereinheitlichen. „Gerade das Aufbereiten der CAD-Daten war sehr aufwändig, da wir Altdaten natürlich nicht bei jedem Releasewechsel mitgezogen haben – allein bringt das keinen Mehrwert“, berichtet Bernd Lehnert. „Bei der Migration nach Inventor wird oft deutlich, dass vorhandene Modelle nicht konsistent sind und im Zuge der Migration zum Beispiel fehlende Referenzen in den Modellen hergestellt werden müssen – was sehr viel Arbeit für die Entwickler bedeutet.“ In der Summe verfügt Rittal zukünftig mit Vault Professional und Inventor über eine Entwicklungsplattform, die sich nicht nur vom EPLAN Engineering Center aus optimal ansteuern lässt, sondern die auch die internationalen Entwicklungs- und Produktionsstandorte gut vernetzt. Der Großteil der Produkte wird zwar in Herborn entwickelt, aber an verschiedenen Standorten weltweit hergestellt. „Ziel ist es, hier eine einzige Datenquelle zu realisieren, so dass alle technischen Daten stets aktuell verfügbar sind“, so Bernd Lehnert abschließend. Die Daten des PDM-Systems werden dazu zwar an den Standorten gespiegelt, aber Vault bringt die Mechanismen für den automatischen Datenabgleich mit sich. „Lokal vorgehalten werden dann nur noch die Daten spezieller länderspezifischer Produkte.“ Autor: Michael Corban, PLM IT REPORT, erschienen in PLM IT Report / 1/12 / November 2
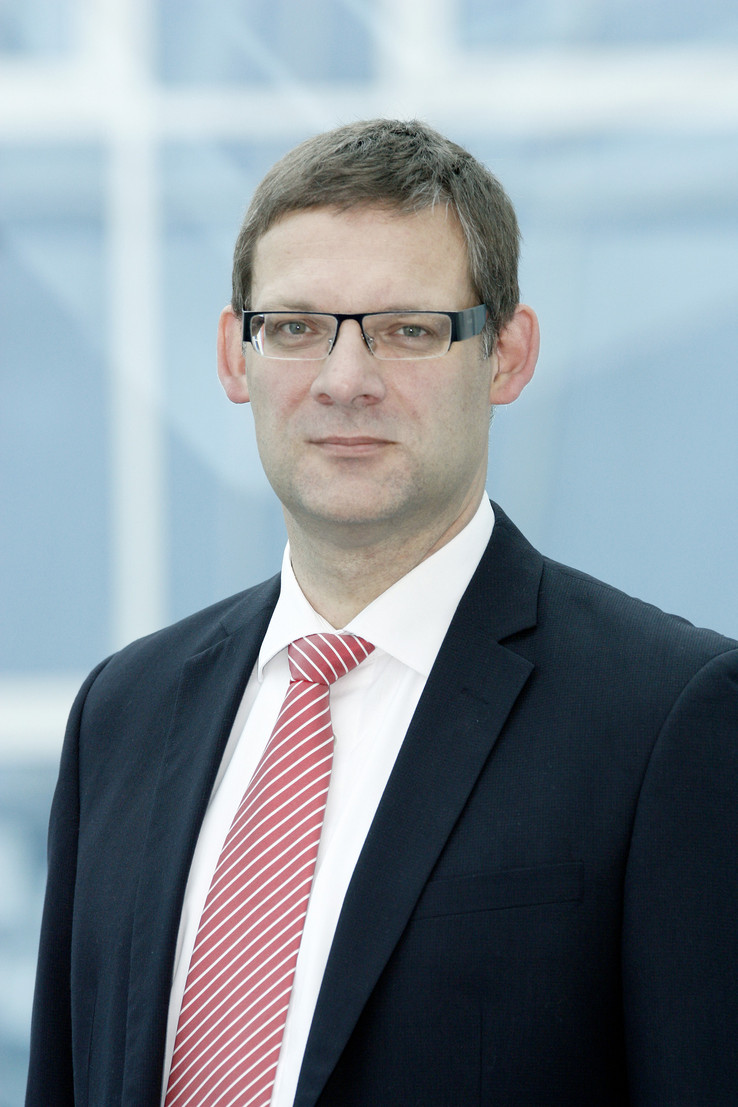
„Wir nutzen das PDM als Datenbank von der Produktentwicklung über das Änderungs- und Revisionsmanagement hinweg bis zum Produktauslauf“, sagt Bernd Lehnert, Abteilungsleiter FuE bei Rittal in Herborn und zuständig für Technologie & Support.
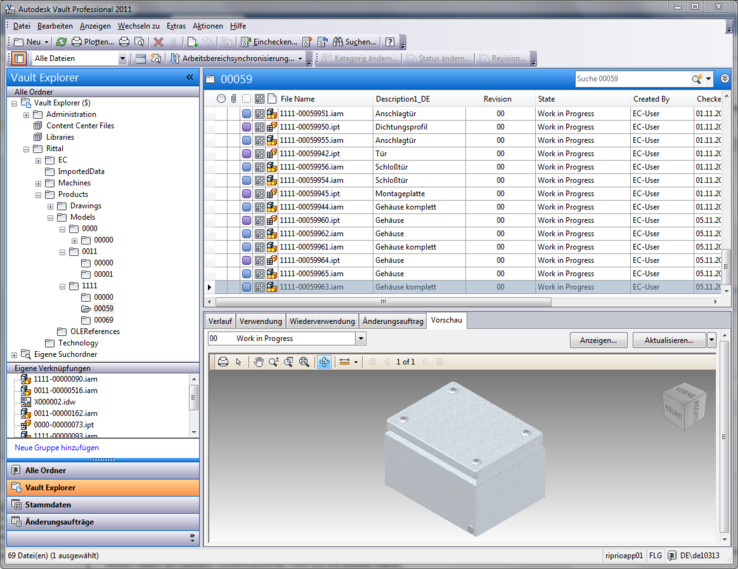
Für die Kompakt-Schaltschränke des Typs AE ist die Konfiguration per Eplan Engineering Center bereits implementiert, in den kommenden zwei Jahren will Rittal diese aber auf alle anderen Produktreihen ausrollen.